Die richtige 3D-Drucktechnologie für Ihr Projekt
Die richtige 3D-Drucktechnologie für Ihr Projekt.
Was Sie auf dieser Seite erwartet.
Unser Ziel: Sie finden schnell & sicher das passende Verfahren – und verlieren keine Zeit mit Recherche.
- Einfacher Überblick über alle Verfahren
- Stärken & Schwächen je Technologie
- Typische Materialien & Bauteilbeispiele
- Vorteile für Sie als Kunde
FDM – Fused Deposition Modeling
FDM ist das bekannteste 3D-Druckverfahren für technische Kunststoffe.
Es basiert auf dem schichtweisen Aufschmelzen und Ablegen von Filamenten (Kunststoffdraht) über eine beheizte Düse. Das Bauteil wird Schicht für Schicht aufgebaut.
Typische Fragen von Kunden, die wir hier beantworten
- Ist das stabil genug?
- Ja – durch Materialien wie PA12, ABS oder CF-verstärkte Kunststoffe können mechanisch belastbare Bauteile gedruckt werden.
- Wie sieht die Oberfläche aus?
- Leicht sichtbar schichtweise, aber auf Wunsch fein abgestimmt. Für Funktionsteile ist es meist perfekt ausreichend.
- Wie groß darf mein Bauteil sein?
- Bis zu 1000 × 1000 × 1000 mm (Unsere Industrieanlagen und Hauseigener Drucker)
- Ist das auch für Serien geeignet?
- Kleinserien sind möglich (z. B. 1000 Stk.), ideal sind Einzelteile, Prototypen & Vorrichtungen.
Branchen, die FDM lieben
- Maschinen- & Anlagenbau (z. B. Gehäuse, Adapter, Halterungen)
- Prototypen- & Vorrichtungsbau
- Elektrotechnik (z. B. ESD- oder flammhemmende Komponenten)
- Startups & Produktentwickler
- Ausbildung & interne Tests
Technische Details
- Schichthöhen ca. 0,08 – 0,5 mm
- Düsenbreite 0,1 – 1,5 mm
- Wandstärke empfohlen min. 3 x Düsenbreite
- Toleranzbereich ±0,3 mm (typisch)
- Max. Bauraum 1000 × 1000 × 1000 mm
- Materialien PLA, PETG, ABS, PA, TPU, CF, ESD, u.v.m.
Ihre Vorteile
- Kostengünstig & schnell
- Mechanisch belastbar
- Große Materialauswahl
- Konstruktionen können sofort getestet & angepasst werden
- Serienähnliche Qualität möglich bei guter Optimierung
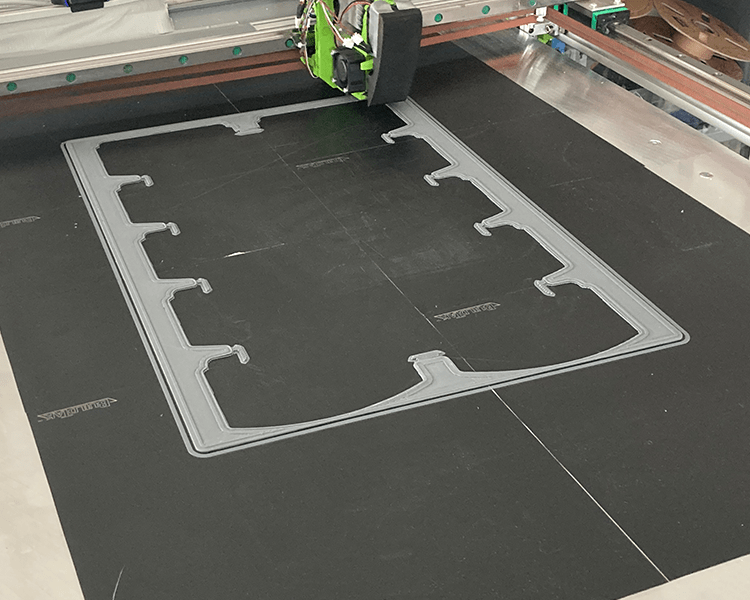
SLA – Stereolithografie
SLA (Stereolithografie) ist ein hochpräzises 3D-Druckverfahren, bei dem ein UV-Laser ein flüssiges Harz Schicht für Schicht aushärtet.
Es liefert extrem feine Details, glatte Oberflächen und ist ideal für Präsentationsmodelle oder medizinische Anwendungen.
Typische Fragen von Kunden, die wir hier beantworten
- Wie präzise ist das?
- SLA liefert Auflösungen von bis zu 25 μm – damit sind selbst kleinste Details sichtbar und messbar.
- Ist es auch stabil?
- SLA ist nicht für schwere Belastung gedacht, aber es gibt technische Harze mit hoher Steifigkeit und Temperaturfestigkeit.
- Wie sieht die Oberfläche aus?
- Die Teile sehen aus „wie gespritzt“. Perfekt für optische Teile, Designmodelle, Formenbau oder medizinische Prototypen.
- Welche Farben / Varianten gibt es?
- Harze gibt es transparent, weiß, grau, schwarz – optional auch elastisch oder temperaturbeständig (bis 120 °C).
Branchen, die SLA lieben
- Medizin & Dental (z. B. Bohrschablonen, Zahnmodelle)
- Produktentwicklung / Design-Agenturen
- Schmuck- und Uhrentechnik
- Startups & Produktentwickler
- Prototyping feiner Geometrien
- Forschung / Mikromechanik
- Automotive
- Werkzeugbau
Technische Details
- Auflösung bis 25 μm (X/Y), 50–100 μm (Z)
- Oberflächenqualität sehr glatt – fast spritzgussähnlich
- Max. Bauraum ca. 800 × 800 × 600 mm
- Materialien Standard-, Technik-, Dental- und Gießharze
- Farben Weiß, Grau, Schwarz, Transparent, Beige
Ihre Vorteile
- Maximal detailgenau – ideal für Prüfmodelle & Design
- Oberflächen wie gegossen – kein Nacharbeiten nötig
- Biokompatible & gießfähige Materialien erhältlich
- Ideal für Visualisierung, Präsentation & medizinische Planung
- Auch feine Hohlräume & scharfe Kanten möglich
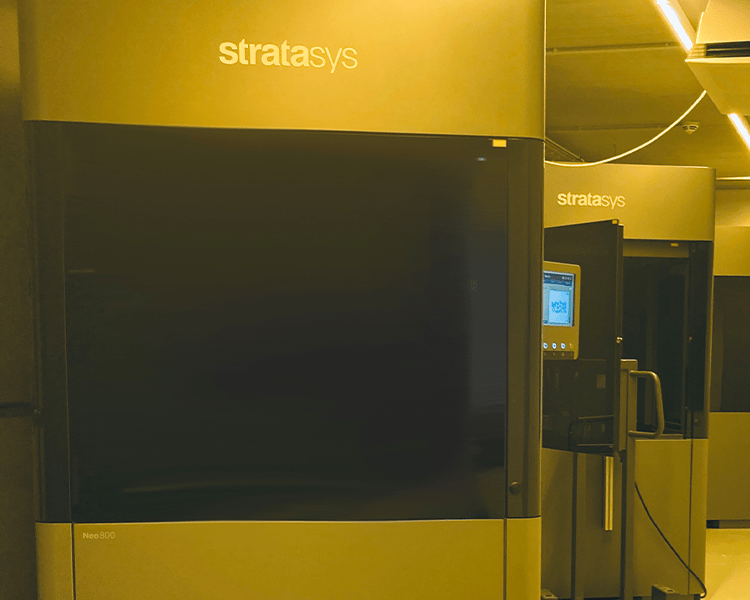
SLS – Selektives Lasersintern
SLS ist ein pulverbasiertes 3D-Druckverfahren, bei dem ein Laser Kunststoffpulver punktgenau verschmilzt.
Das Bauteil entsteht schichtweise im Pulverbett – ohne Stützstrukturen. Dadurch sind komplexe Geometrien, Hohlräume und Serienfertigungen besonders effizient umsetzbar.
Typische Fragen von Kunden, die wir hier beantworten
- Ist SLS wirklich stabil genug für echte Funktionsteile?
- Ja! Mit Materialien wie PA11 oder PA12 sind belastbare, langlebige Bauteile möglich – z. B. für Automotive, Maschinenbau oder Robotik.
- Muss ich bei SLS mit Stützstrukturen rechnen?
- Nein! Das Pulverbett stützt das Bauteil selbst – keine Supportstrukturen notwendig, keine Nachbearbeitung durch Supportentfernung.
- Wie sehen die Oberflächen aus?
- Leicht rau, ähnlich sandgestrahlt – ideal für funktionale Anwendungen. Auf Wunsch können die Teile geglättet, gefärbt oder lackiert werden.
- Wie groß darf mein Bauteil sein?
- Bis zu 230 × 230 × 400 mm oder 315 × 208 × 293 mm
- Lohnt sich SLS bei Einzelstücken?
- Ja! Gerade funktionale Einzelteile oder Prototypen sind typische SLS-Cases. Ab ca. 1–5 Stück bist du wirtschaftlich dabei – ab 10+ geht’s in Serie!
Branchen, die SLS lieben
- Maschinenbau & Automotive (z. B. Halter, Gehäuse, Lüfterkanäle)
- Medizintechnik (z. B. anatomische Modelle, OP-Hilfen)
- Robotik, Drohnen & Luftfahrt
- Forschung & Leichtbau
Technische Details
- Auflösung / Genauigkeit ±0,2–0,3 mm (materialabhängig)
- Bis zu 230 × 230 × 400 mm oder 315 × 208 × 293 mm
Ihre Vorteile
- Komplexe Geometrien ohne Stützstruktur
- Gleichbleibende Qualität bei Kleinserien
- Hohe Festigkeit & Temperaturstabilität
- Besonders geeignet für bewegliche Teile und Lastaufnahmen
- Schnellere Durchlaufzeit durch parallele Druckjobs
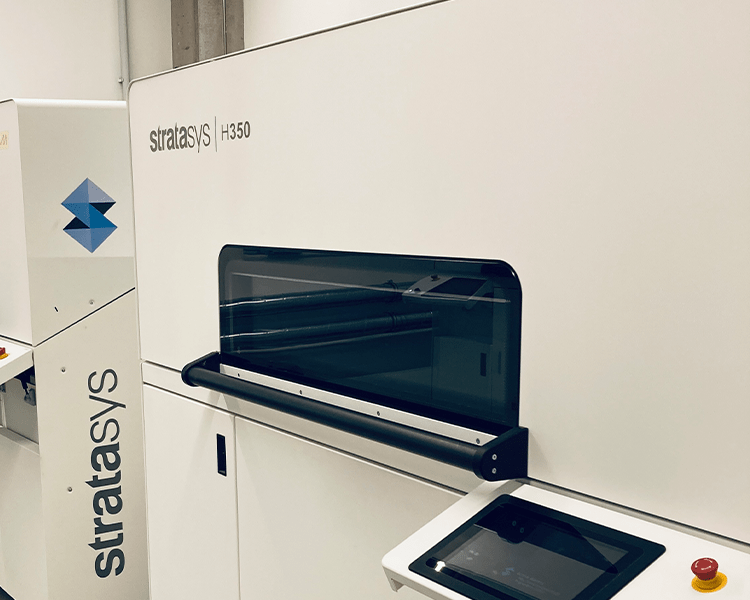
PolyJet – Präzise. Mehrfarbig. Multimaterial.
PolyJet ist ein hochpräzises 3D-Druckverfahren, das ähnlich wie ein Tintenstrahldrucker funktioniert – nur mit photopolymeren Kunststoffen.
Flüssige Materialien werden Schicht für Schicht aufgetragen und sofort mit UV-Licht gehärtet. Mehrere Materialien, Farben und sogar Transparenzen können in einem Bauteil kombiniert werden.
Typische Fragen von Kunden, die wir hier beantworten
- Wie realistisch kann ein Modell sein?
- PolyJet kann hautähnliche Texturen, Organe, Knochen, Knorpel und sogar transparente Adern darstellen – perfekt für OP-Planung oder Patientengespräch.
- Kann ich verschiedene Materialien in einem Bauteil kombinieren?
- Ja! Mit PolyJet sind Hart-Weich-Kombinationen, Gummiähnliche Bereiche, transparente Segmente und Farbeffekte in einem einzigen Modell möglich.
- Wie fein ist die Auflösung?
- PolyJet ist das präziseste Polymerverfahren – Auflösung bis 14 μm (X/Y), Schichtstärken bis 16 μm.
- Ist es auch funktional belastbar?
- Nicht primär. PolyJet ist stark in der Darstellung, bei moderater Funktion. Für rein technische Belastungen eignet sich z. B. SLS oder FDM besser.
Branchen, die PolyJet lieben
- Medizintechnik (OP-Planung, Implantatvisualisierung)
- Dentaltechnik
- Produktdesign / Prototyping
- Forschung & Lehre
- Marketing / Messemodelle / Architektur
Technische Details
- Auflösung bis zu 14 μm (X/Y)
- Schichtdicke 16–32 μm
- Materialien Vero™, Agilus™, Digital Anatomy™, Tango
- Farben CMYKW + transparent + digital mixed (Pantone)
- Shore-Härten 30A – 95A simuliert
Ihre Vorteile
- Extreme Detailgenauigkeit – feinste Strukturen & Konturen
- Farbige, transparente, elastische & harte Materialien kombinierbar
- Ideal für realistische Medizinmodelle & Präsentationen
- Sofort einsatzfähig – ohne Nachbearbeitung
- Hoher Eindruckfaktor bei Präsentation, Schulung & Kundenkommunikation
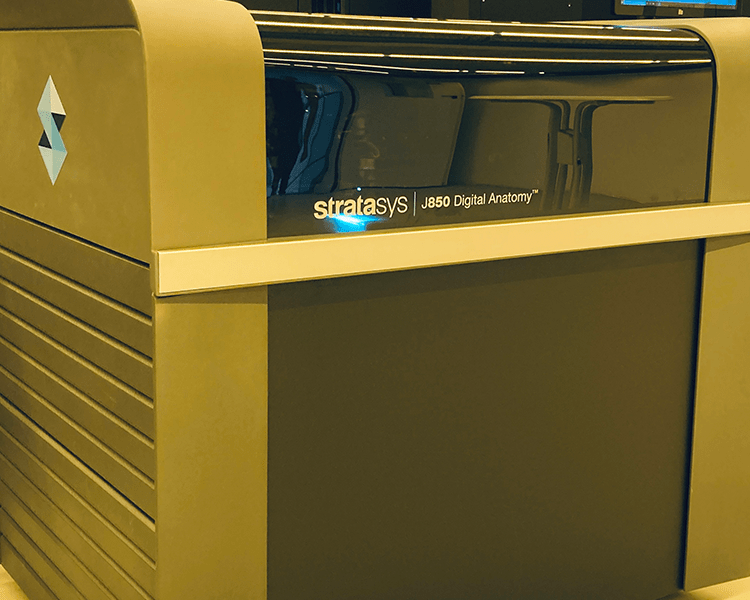
DED – Directed Energy Deposition
DED ist ein metallisches 3D-Druckverfahren, bei dem Draht oder Pulver gezielt mit einem Laser aufgeschmolzen und schichtweise aufgetragen wird – oft auf bestehenden Bauteilen.
Das drahtbasierten DED-System, das sich besonders für hybriden Metallbau eignet.
Typische Fragen von Kunden, die wir hier beantworten
- Ist das wirklich echtes Metall?
- Ja – z. B. Edelstahl 316L, Inconel, Titan, Werkzeugstahl. Die mechanischen Eigenschaften sind mit klassischer Metallbearbeitung vergleichbar.
- Wie sieht die Oberfläche aus?
- Rohzustand: rau & wellig – wird meist gefräst, geschliffen oder CNC-nachbearbeitet. Wir bieten DED inkl. Nachbearbeitung (wenn gewünscht).
- Welche Genauigkeit ist möglich?
- Ca. ±0,5 mm im Rohdruck – Feinformen oder Passungen entstehen durch Nachbearbeitung. DED ist ideal für „funktionale Grobgeometrie + Finishing“.
Branchen, die DED lieben
- Maschinenbau & Werkzeugbau
- Automotive (z. B. Sensorhalter, Gussteilerneuerung)
- Luftfahrt (z. B. Wartung / Repair / Overhaul)
- Energie & Öl / Gas
- Forschung (z. B. Multi-Material-Aufbau)
Technische Details
- Auflösung (Schichtdicke) 0,3 – 0,9 mm (Draht-basiert)
- Genauigkeit ±0,3–0,5 mm (nachbearbeitbar)
- Materialien Edelstahl, Inconel, Titan, Werkzeugstahl u. a.
- Nachbearbeitung Optional z. B. CNC-Fräsen
- Besonderheit Hybridfähiges System – kombinierbar mit CNC-Maschinen
Ihre Vorteile
- Metallteile ohne Gussform oder Vorrichtung
- Materialkombination in einem Bauteil möglich
- Hybridfertigung (z. B. auf Fräskörper aufbauen)
- Extrem hohe Materialeffizienz – nahezu kein Verschnitt
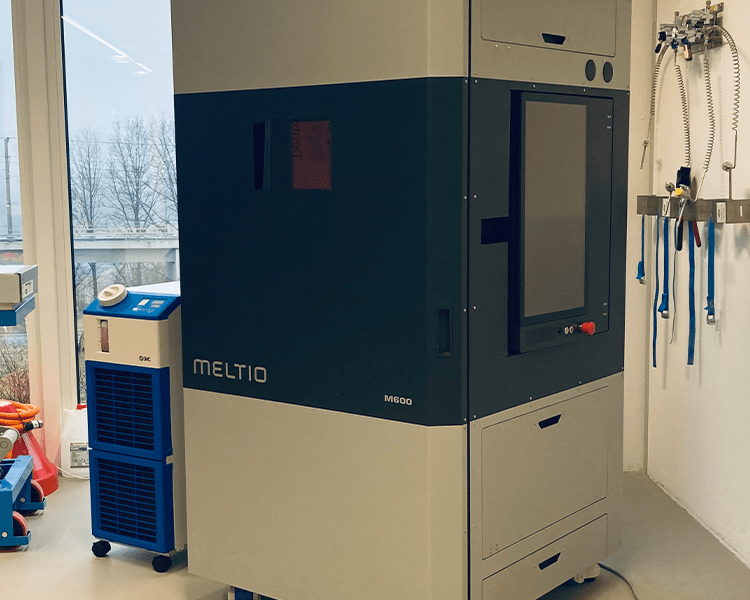
Weitere Fragen? Wir sind persönlich für Sie da
Wir wissen: Additive Fertigung ist für viele noch neu – und diese Seite enthält viele Informationen. Statt sich durch alles zu klicken, können Sie uns auch direkt kontaktieren. Stellen Sie uns einfach Ihre konkrete Frage:
Über das Kontaktformular → Wir antworten schnell & konkret
Telefonisch → Persönliche Beratung mit technischem Verständnis
- Kein Callcenter – Sie sprechen mit echten Menschen vom Fach
- Ehrlich, verständlich & lösungsorientiert
- Auf Wunsch inkl. Rückrufservice
Oder senden Sie uns Ihre Datei und schreiben Sie dazu, worum es geht – wir empfehlen Ihnen die passende Technologie.